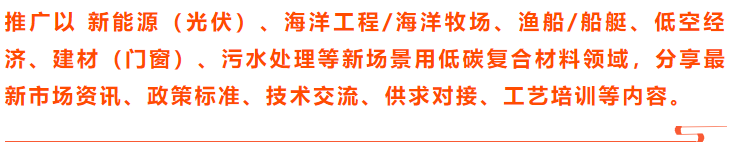
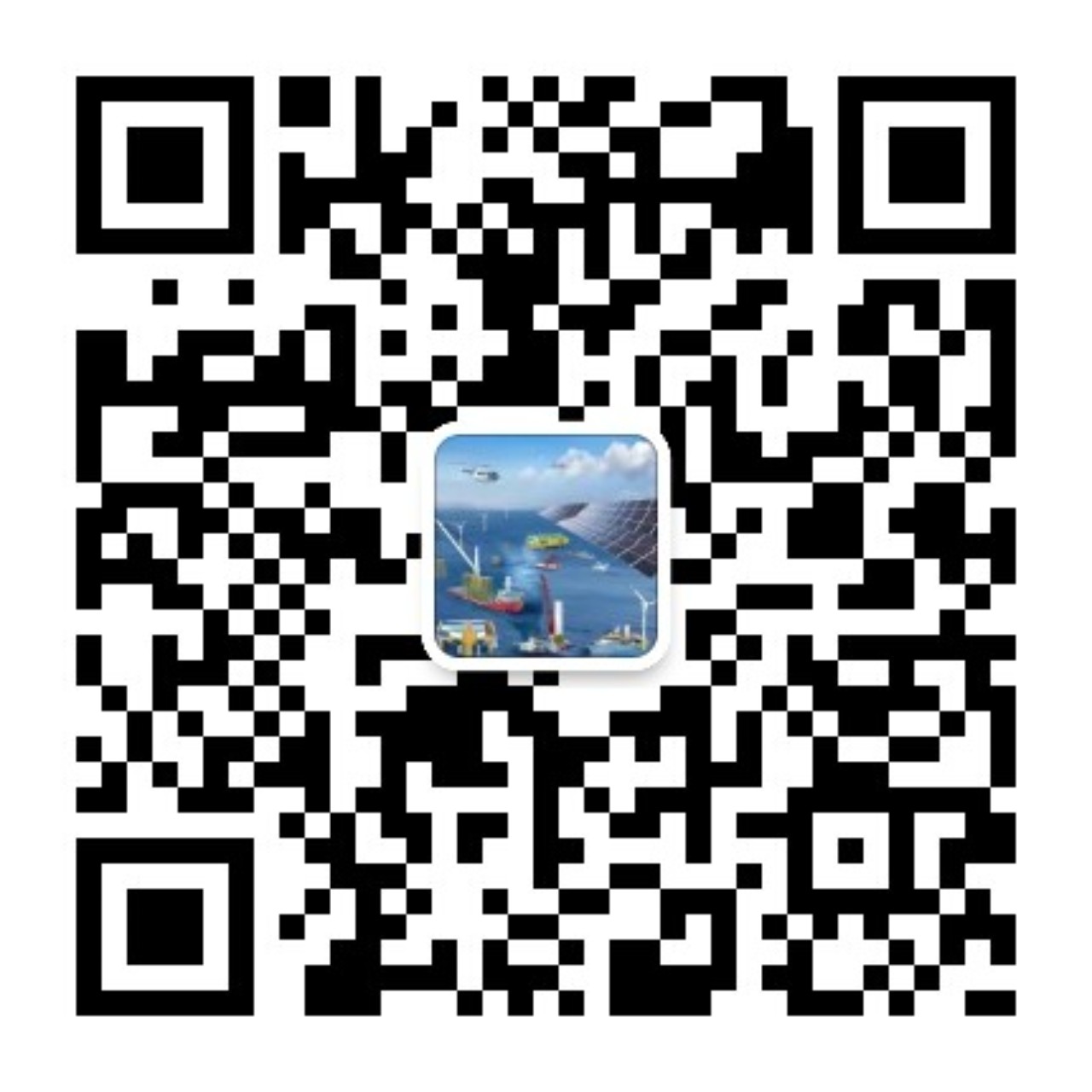
转载说明:本文转自MDPI仅用于专业知识的分享与交流,如任何组织/个人对版权或真实性、准确性存在质疑,请与我们联系进行删除/修改;文中内容由翻译软件翻译,如有错误请您海涵!
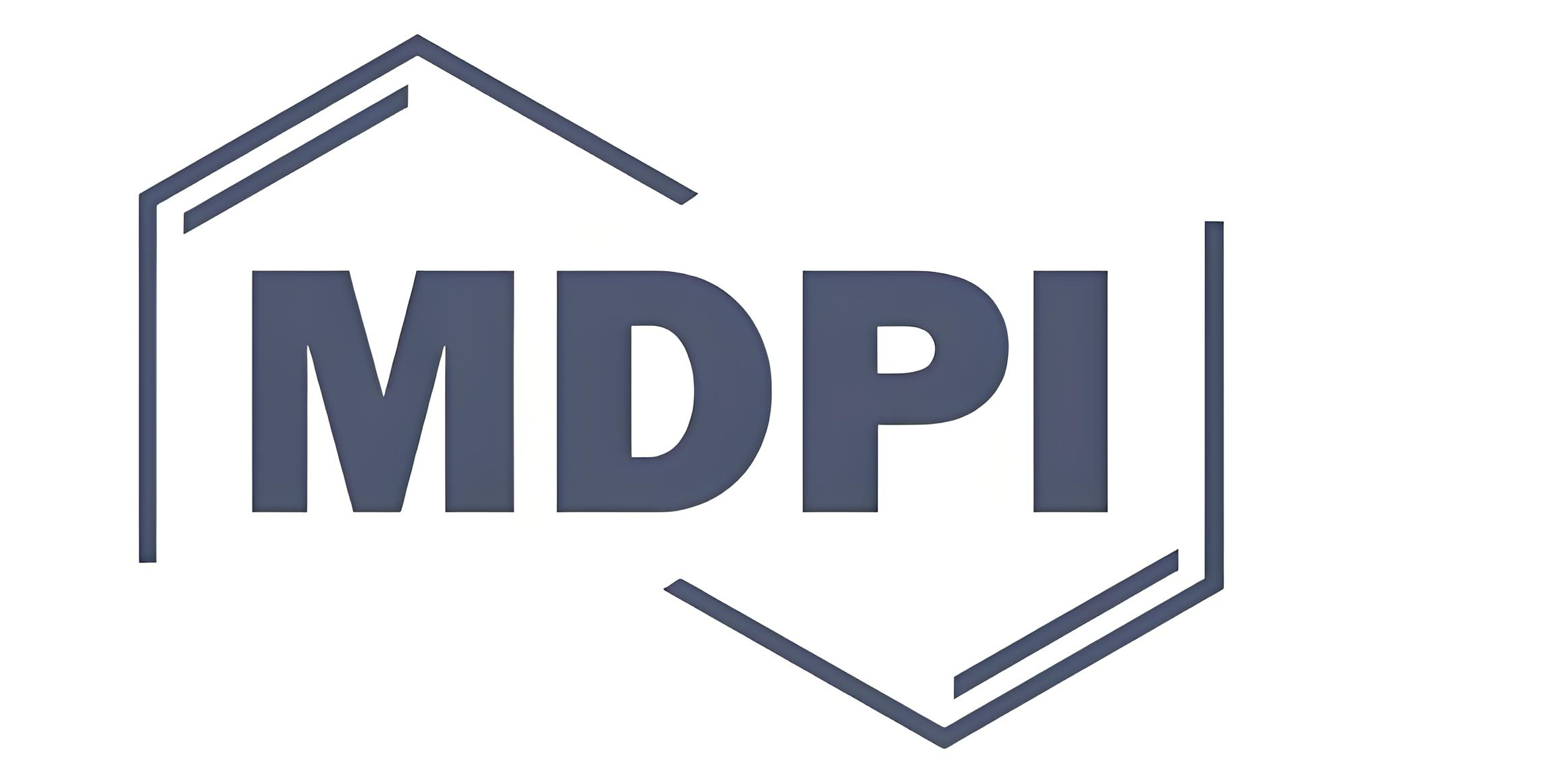
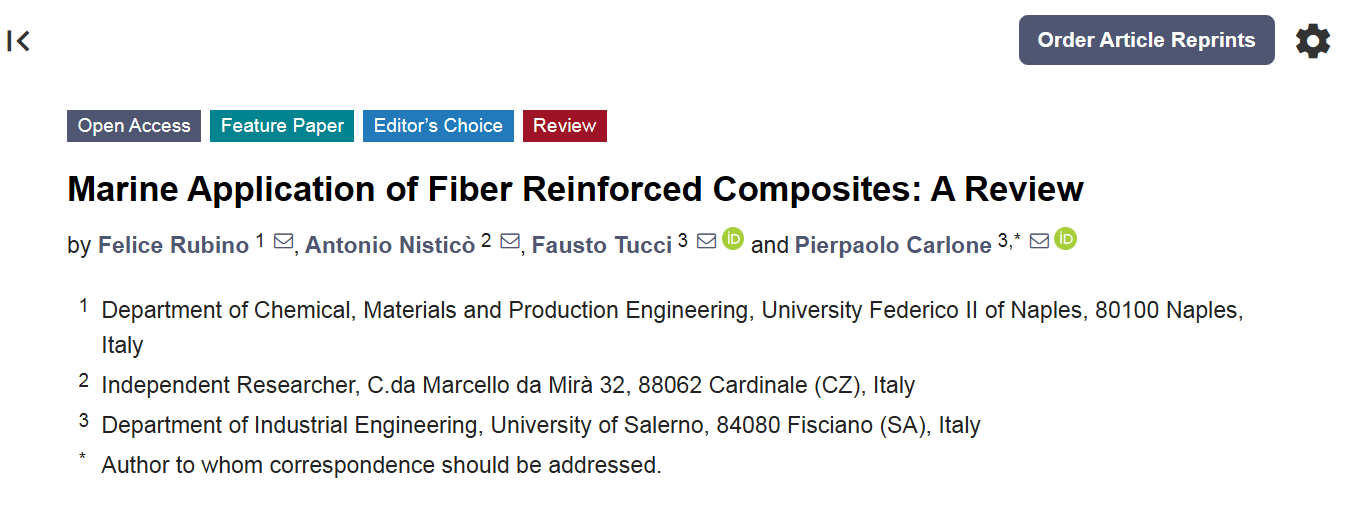
在海洋环境中工作的部件和结构会受到风、浪和潮汐作用产生的高应力。此外,它们在其使用寿命期间必须面对恶劣和严酷的环境条件,甚至可能被置于浪花区或浸没在盐水中。过去几十年来,聚合物复合材料在海洋系统中的应用一直是深入研究的重点,突出了更换船体、螺旋桨叶片、风力涡轮机和潮汐涡轮机叶片等多个部件带来的潜在好处。本文报告了该领域的进展,介绍了先进复合材料在船舶和船舶部件、海上石油和天然气复合材料、海洋可再生能源和水下修复中的应用。1. 简介
船舶、潜水器、海上结构和其他海洋结构部件都面临着相关的环境挑战。因此,人们通常考虑使用具有高抗性且在较长时间内几乎不需要维护的材料。此外,为了满足设计要求并快速可靠地运行,船舶必须具有轻质和耐腐蚀性。复合材料,特别是纤维增强聚合物 (FRP),在二战后被广泛用于海洋工业,当时复合材料旨在克服钢、铝和木材的腐蚀问题。减轻重量曾经是、现在仍然是一个关键方面,特别是对于商用船舶的顶部重量。多年来,复合材料的发展满足了海洋部门日益增长和变化的需求,仍然保留了制造综合元件的相关用途,包括格栅、管道、轴、管路和船体外壳。到目前为止,复合材料已应用于海洋领域的所有领域,用于各种部件和结构,即船体、轴承、螺旋桨、舱盖、排气装置、顶部结构、机鼻雷达罩、声纳罩、栏杆、所有类型的船舶、阀门和其他海底结构。近年来,复合材料制成的赛艇越来越普遍,因为它们具有持久的高性能和安全性。盐和腐蚀性海水对船舶和建筑物的破坏性尤其大。鉴于复合材料具有抗腐蚀和抗疲劳的能力,通过在特定部件(如固定件和连接器)中使用热固性复合材料可以显著减少维护要求。使用热固性树脂作为基质材料通常与以下方面有关:- 机鼻雷达罩和声纳罩的声学透明度高,增强刚度以提高稳定性
复合材料科学和技术发展迅速,提供了新的材料解决方案,满足了高性能的要求。在下一节中,我们将回顾该领域的发展现状。航海业经历了显著的技术变革,如今,船体制造基于最新一代生产系统。先进复合材料的引入代表了船舶制造领域的里程碑式创新。复合材料技术使制造商能够提高产品质量,获得坚硬而轻便的结构,从而提高航行性能和使用寿命。此外,由于可以实现自动化和加快制造过程,复合材料的采用降低了总成本,使最终产品为更多公众所接受 [ 1、2、3 ]。刚性更高的船体和甲板是造船业采用复合材料夹层结构的主要应用,这种结构由放置在部件外表面上的两层具有高刚度和强度的外皮以及柔软而厚的芯层组成。坚硬的外皮具有较高的弯曲刚度,同时,芯层可支撑剪切应力和压缩应力并稳定外皮,防止整体和局部不稳定。重量减轻可增加载货容量、节省燃料、降低惯性并提高船舶稳定性和浮力。此外,FRP 在海洋环境中表现出令人满意的耐腐蚀性能,并且维护需求较少。在船舶夹层结构中,芳族聚酰胺、碳纤维和玻璃纤维增强复合材料通常用作外皮,替代金属。聚合物泡沫(即聚苯乙烯和聚氯乙烯 (PVC))和蜂窝状材料主要用作芯材。芳族聚酰胺纤维(如 Kevlar)或碳纤维的组合可增强高质量树脂和超轻芯材(如 Nomex),从而使船舶具有无与伦比的机械性能和尺寸。另一方面,与传统材料相比,复合夹层结构成本更高,制造工艺更加劳动密集,限制了它们的广泛应用[ 1,4 ]。玻璃钢 (GRP) 首次应用于海军造船业可追溯到 1973 年,当时的扫雷舰 (MCMV) HMS Wilton 长 60 m,满载 725 吨。该舰由 Vosper-Thornycroft 公司制造,并于 1975 年由英国海军批量生产。事实证明,GRP 舰船能够承受海洋中的极端工作条件以及撞击和火灾 [ 5 ]。英国海军随后的“桑当”级项目旨在减轻重量以增加武器容量并降低成本,以提高项目的国际竞争力。对超大部件进行了重新设计(可接受地降低了安全裕度),但仍保持了可接受的可靠性。此外,还拆除了框架和船体之间的螺栓。1975 年,法国、比利时和荷兰联合启动了一项研发计划,旨在建造 40 艘舰艇,由参与国共享技术。具体来说,主要机械、辅助机械和武器装备分别由荷兰、比利时和法国公司制造[ 5 ]。DCN Diving 公司提供造船技术,使用 GRP 制造船体、甲板和隔板,使用销钉连接船体和加固结构。1970 年至 1984 年间,瑞典卡尔斯克鲁纳造船厂开发的 GRP MCMV 采用了由 GRP 蒙皮和 PVC 泡沫芯组成的夹层结构。该技术解决方案满足了抗疲劳性、非磁性行为以及经济技术可行性的要求。其他示例包括澳大利亚皇家海军使用夹层结构(泡沫芯和 GRP 蒙皮)生产 MCMV 双体船体。HMAS Rushcutter 的船体采用 60 mm 厚的高密度 PVC 泡沫芯和 8 mm 厚的 GRP 实现。更具体地说,蒙皮板采用短切毡和编织粗纱增强材料组合制造,以最大程度地提高粘结强度、耐火性和层间剪切强度。图 1报告了主要三类舰船完全使用复合材料生产的舰船长度多年来的演变情况 [ 5 , 6 ]。图 1. 全复合材料巡逻艇、扫雷艇(MCMV)和轻型护卫舰的长度与建造年份关系图 [ 5 ]。护卫舰是目前使用玻璃钢建造的最长的舰船。在这一领域,瑞典海军在 YS-2000 项目框架内设计和实现的多用途维斯比护卫舰是复合材料应用的典范。维斯比号长 72 米,宽 10.4 米,满载 620 吨,是舰队中最大的舰船之一。它专为监视、作战、扫雷、对抗和反潜作战而设计。维斯比护卫舰完全采用复合材料设计,使用碳和玻璃增强夹层板和乙烯基树脂基质。事实上,复合材料具有坚固性、抗水下冲击载荷和低磁容量以及轻质特性。维斯比号是第一艘船体中大量使用碳纤维复合材料的舰船。尽管碳纤维的成本至少比玻璃高出五倍,限制了其在大型船舶结构中的使用,但研究发现,通过在复合材料中使用一些碳纤维,除了足够的电磁屏蔽外,船体的重量还可以减轻约 30%,而不会显著增加制造成本。减轻重量意味着减少燃料消耗[ 2、5、7 ]。新加坡皇家海军和瑞典 Kockums AB 造船厂设计了新一代轻型护卫舰,称为新一代巡逻舰(NGPV)级,由 FRP 制成。设计船长 80 m,满载重量为 1016 吨。复合材料设计和制造技术的发展导致船舶长度稳步增加,目前,全复合材料船舶长度可达 80/90 m。最近研究预测,到 2020 年,完全由复合材料制成的中型战舰船体长度很容易达到 120/160 m[ 4 ]。然而,由于制造成本低且可靠性更高,传统材料(铝和钢)仍是轻型护卫舰的主要选择[ 8 ]。美国海军首次在“Guppy”级潜艇的指挥塔上采用了完全由玻璃钢制成的导流罩。这些部件传统上由铝制成,易遭受严重腐蚀,需要持续不断的维护和维修。复合材料导流罩更加耐用,维护需求减少。因此,在 1950 年至 1970 年间,有 25 艘以上的 Guppy 级潜艇配备了复合材料结构。复合材料还考虑用于加压潜艇的内部应用,包括舱壁、甲板、舱口、主推进轴、压载水箱、水箱、机器、泵、阀门和管道 [ 4 ]。图 2总结了目前使用或正在开发复合材料的军用舰船和潜艇上的应用 [ 1、5、6 ]。图 2. 纤维增强聚合物(FRP)结构在海军舰艇和潜艇中的军事应用 [ 4 ]。除战斗舰艇外,高性能材料现在也应用于民用领域。玻璃钢在世界各地用于生产渔船、小船、气垫船和双体船。就现役玻璃钢船只数量而言,日本是目前领先的国家。1984 年,日本玻璃钢渔船占注册船只总数的 60%,其中一些船体长度达 45 米。除日本外,欧洲和澳大利亚的造船厂也生产大型玻璃钢渔船[ 1、5、6 ]。玻璃钢在小型船舶上的应用包括游艇、帆船、驳船和救生艇。对于长度不超过 20 米的船舶,玻璃钢是主要使用的材料,约占船体的 80%。与钢材相比,玻璃钢材料在减轻重量和降低生产成本方面具有显著优势,而且由于其对海洋生物和腐蚀的抵抗力显著提高,维护成本也最低。荷兰“Mulder and Rijke”造船厂开发出了一种具有高阻燃性能的玻璃纤维/聚氨酯复合材料救生艇。在耐火试验中,救生艇浸入火焰中 10 分钟:外部温度为 1500 °F (816 °C),而内部温度仅为 15.5 °C [ 9 ]。长期以来,气垫船一直是纤维增强塑料在海洋领域的主要应用。例如,1969 年制造的 Hovermarine HM2 的 15.5 米船体采用夹层结构,该结构由纤维增强复合材料层压板与 PVC 和聚酯泡沫芯制成。1984 年推出的 Vosper Hovermarine 的 HM221 渡轮的首款 24 米船体完全采用夹层结构建造,船体采用 GRP 外皮和 PVC 泡沫芯,饰面采用 GRP 面板。最近,挪威 Brodrene 公司使用 GRP 夹层建造了 SES Norcat,该船长 32.2 米,总吨位 290 吨,最高时速 42 节 [ 5 ]。双体船主要用于快速渡轮、近海和海洋航行船以及小型游艇,因为它具有良好的载客量、燃油效率和高可靠性。1985 年在挪威推出的 CIRR 27P CAT(长 27 米,载客量为 184 名乘客)是第一艘使用玻璃钢制造的船舶。挪威船舶服务公司 Verft 使用芳纶增强夹层板生产了一系列多用途侦察船,尺寸从 23 米到 38 米不等。芳纶纤维层压板(外皮)和 PVC 泡沫(芯)的组合使船体的抗拉强度比钢高出五倍,并降低了噪音,这对于地震调查作业至关重要。碳纤维增强材料也用于双体船和三体船的生产。第一个例子是 1976 年制造的一艘 24 米长的三体船。碳纤维的后续应用是三井工程和造船公司使用混合碳玻璃增强材料建造的 Cruiser 半潜式双体船[ 4 , 10 , 11 ]。就船舶部件而言,FRP 主要应用于桅杆和螺旋桨。复合材料在舰船桅杆建造中的应用始于 1990 年,当时的一项初步研究表明,使用复合材料可以解决使用钢材时遇到的多个问题[ 5 ]。复合桅杆的首批原型之一是用混合玻璃/碳纤维复合材料制造的,目的是提高防弹性能和刚度。研究报告称,与同尺寸的铝制轴相比,复合材料轴的重量减轻了 20±50% [ 4 ]。复合材料轴具有更好的抗疲劳和抗腐蚀性能,还能提供减振和抗气流冲击损伤性能。另一方面,复合材料轴的成本比传统轴增加了 50%。1995 年,美国海军启动了先进封闭式桅杆/传感器 (AEM/S) 计划,以开发下一代舰船桅杆。AEM/S 系统高 28 米,直径 10.7 米,呈六边形,是当时美国海军舰艇上最大的复合材料结构。独特的设计,加上增强材料的混合特性,提高了天线和传感器的性能,同时仍保持了可接受的雷达截面[ 5、12 ]。英国皇家海军和 Vosper Thornycroft 造船厂于 1996 年使用 FRP 建造了综合技术桅杆 (ITM)。与 AEM/S 项目类似,ITM 由夹层结构组成,通过重新设计形状来减少电磁干扰,与钢桅杆相比,重量又减轻了 10/20%。ITM 提高了军舰的隐身能力,与传统钢天线相比,它提供了更好的环境和电磁屏蔽。ITM 技术自 2011 年起开始在舰船上安装 [ 13 ]。在德国,空心轴是将多层连续玻璃和碳纤维浸入环氧树脂中,缠绕在木质/铝质主轴上制成的[ 13 ]。船舶和潜艇中的螺旋桨通常由镍铝青铜 (NAB) 合金制成,因为该合金具有出色的耐腐蚀性和高屈服强度。另一方面,由于形状复杂,用 NAB 合金制造螺旋桨叶片的成本很高,而且一些与声阻尼性能差导致振动噪音过大有关的问题尚未解决。这些限制促使海军工程师评估使用 NAB 合金替代材料制造螺旋桨叶片的可行性,其中最值得关注的候选材料是不锈钢、钛合金和 FRP [ 4,14 ]。复合材料螺旋桨叶片通常由玻璃或碳纤维层压板制成,而薄层聚氨酯或 NAB 或不锈钢可用于减少叶片的冲击损伤。FRP 叶片通常粘合或固定在螺旋桨的金属轮毂上,尽管复合材料轮毂也已实现。早期的复合材料螺旋桨直径可达 2 米,于 20 世纪 60 年代在苏联渔船上进行了测试,然后在 20 世纪 70 年代初被引入大型商船,直径约为 6 米。同年,此类部件的原型应用在气垫船上进行了测试。复合材料螺旋桨在航行速度、燃料消耗、发动机工作负荷和使用寿命方面与金属螺旋桨性能相似。此外,它们将发动机和传动轴的共振振幅降低了约 25%,从而降低了船体振动和噪音。另一方面,与 NAB 制成的螺旋桨相比,复合材料螺旋桨的制造成本更高、叶片尖端偏差较大、抗冲击性较低 [ 5 ]。除了桅杆和螺旋桨之外,如今一些次要部件(尤其是军舰中的部件)也使用聚合物复合材料代替金属制造。例如,舵、舱壁、甲板和舱口、排放漏斗、防护系统和防护罩、发动机部件和热交换器。船舶制造商需要具有良好热性能和机械性能的树脂,同时在制造复合材料部件时易于加工。合适的树脂应易于层压、室温固化并与增强材料兼容。乙烯基酯的机械性能和价格介于聚酯和环氧树脂之间。由于存在酯基,它们与聚酯具有良好的亲和性,并且与聚酯类似,乙烯基酯在室温下需要催化剂和促进剂才能固化[ 8、15 ]。由于反应位点较少,乙烯基酯具有良好的耐化学腐蚀性能,并且在吸收和水解侵蚀方面表现出可接受的行为。由于这些原因,它们成为船体材料中有吸引力的选择[ 1、2、3、11、15 ]。玻璃/聚酯层压板上的乙烯基酯基表皮能够防止水解引起的渗透性起泡。船舶制造商或船主可以采用这种保护措施,而不是更昂贵的环氧树脂,即使后者是更有效的防潮屏障。乙烯基酯比聚酯更柔韧,硬度更高。因此,如果用作 FRP 层压板中的基质,它们可以更好地抵御疲劳导致船体和甲板失效的影响。乙烯基酯的工作温度相对较高,最高可达约 200°C。不列颠哥伦比亚省 West Bay SonShip 率先推动了这一转变,用乙烯基酯代替聚酯树脂来生产其游艇中的 GRP 组件。由于乙烯基酯具有良好的弹性,它越来越多地用于建造大型船舶,包括军舰。瑞典 Visby 级护卫舰采用乙烯基酯/碳夹层船体和 PVC 芯。另一方面,与聚酯相比,乙烯基酯的加工难度更大,因为必须仔细准备表面并在处理过程中保持特定的环境条件才能实现纤维和树脂之间的良好粘合。此外,如今,树脂必须具有较低的苯乙烯含量才能满足更严格的工业排放法规[ 11、15、16 ]。历史上,FRP 船舶一直采用手工铺层或喷射工艺建造。或者,建造者采用预浸渍织物生产高质量的复合材料船体。这种方法成本较高,但生产时间较短,浪费较少。上述方法通常考虑使用聚酯 (PE) 和乙烯基酯 (VE) 树脂来实现船舶结构。这些材料具有良好的防水性、固化时间短且易于层压。然而,PE 和 VE 的收缩率高 (7–10%),苯乙烯排放量高,需要专用系统来最大限度地减少工人的接触 [ 1、3、16 ] 。如今,新型闭模和灌注工艺的发展推动了先进环氧树脂在船体生产中的应用。环氧树脂确实显著提高了船舶的质量和性能,并消除了危险排放,正如美国和欧盟的政府法规所规定的那样。环氧体系也为造船商带来了技术优势。它们黏度较低,可在低温下固化,特别适合无需高压釜固化的灌注工艺。环氧树脂的伸长率、拉伸强度和模量均高于 PE 和 VE。因此,设计人员可以增加纤维含量并减少层压板的层数,而不会损害船体的机械性能。实现的重量减轻可保证更高的速度并降低燃料消耗。此外,由于固化收缩率降低(小于 2%),可直接在模具上实现光滑的表面。许多生产商,如 Huntsman and Scout Boats, Inc.(南卡罗来纳州萨默维尔)都已从环氧树脂的使用中受益。这艘 2015 年采用灌注工艺制造的 42 英尺运动渔船可视为减轻重量、改善流体动力学性能的一个例子[ 11,16 ]。聚酯树脂和环氧树脂被广泛用作 FPR 结构的基质。尽管如此,据报道酚醛树脂取得了重大进展。酚醛树脂的耐火性尤其突出,因为它们在相对较高的温度下(约 200°C)仍具有耐火性,并且烟雾或有毒气体排放量低。它们可以通过多种方法加工,包括手工铺层、热压、灌注。相比之下,它们的机械性能比聚酯低10-20 % [ 1、2、3 ]。玻璃纤维是大型复合结构中最常用的材料,但航空航天领域的一些应用除外。根据玻璃的类型、长丝直径、纤维尺寸和化学性质,可以实现各种特性和性能。表 1报告了市场上不同类型玻璃纤维的物理和机械性能。海洋应用中最常见的增强材料仍然是 E 玻璃纤维,它具有良好的最大拉伸强度(约 2200 MPa)和极限拉伸应变(约 2.5%),同时具有出色的防潮和防化学侵蚀性能。由于其化学成分,E 玻璃具有出色的电绝缘性能。高强度玻璃的玻璃纤维在美国通常称为 S 玻璃,在欧洲称为 R 玻璃,在日本称为 T 玻璃。S 玻璃的 SiO2、Al2O3 和 MgO 含量较高,通常比 E 玻璃高 40-70%。当温度从 70 °F(室温)升高到 1000 °F(约 540 °C)时,E 玻璃和 S 玻璃的拉伸强度都会损失一半,即使这两种纤维类型仍然具有良好的耐受性 [ 11,17,18 ]。碳纤维的强度和刚度高于玻璃纤维。碳纤维的最大拉伸强度约为 4000 MPa,断裂伸长率为 0.9–2%,具体取决于碳纤维的类型(见表1)[ 19 ]。然而,这些纤维的成本远远超过玻璃纤维,因此完全由碳纤维制成的结构并不容易负担,船舶设计师发现使用由碳纤维和玻璃纤维制成的混合层压板非常有吸引力。尽管如此,从设计的角度来看,碳纤维复合结构更方便,而且从总体成本(原材料和制造成本)来看也更具成本效益。事实上,可以减少增强材料的数量,从而平衡碳纤维的高价格,而不会降低结构性能。海上设施的主要功能是从海底开采原油,同时尽量减少对海底形态的影响,并最大程度地尊重安全和环境保护要求。开采出的原油随后被运输到沿海的工厂,经过处理后再出售。由于海上建筑成本高昂,尽可能减少和简化公海设施至关重要。此外,在较深的水域(从 300-400 米到 2000 米)设计和安装新的生产工厂不能依赖于浅水区采用的标准技术解决方案。石油和天然气行业的研究人员和工程师正在放弃刚性固定结构,转而采用浮动结构(仍然锚固在海底建造的开采结构上)。在这种情况下,较大的位移可以提供对波浪运动的必要适应性。此外,为了最大限度地降低工厂要求和施工阶段的成本,建筑商正在推动预制多个元素,尽可能限制海上施工工作。石油和天然气行业开始将先进复合材料视为一种可行且经济高效的金属替代品,因为与金属相比,复合材料具有更高的耐腐蚀性、高刚度和强度以及更轻的重量。FRP 在该领域的典型应用包括刚性管道、缠绕管道、刚性和柔性立管、结构修复等 [ 20 ]。玻璃纤维是用于生产复合管道的最广泛的材料,该管道用于将石油或天然气从近海钻井站输送到陆上工厂[ 21 ]。然而,当输送的流体是高压天然气时,玻璃钢管道的使用并不常见。玻璃纤维管通常采用两种生产方法制造:纤维缠绕(手动或自动)和离心铸造。在纤维缠绕工艺中,管的内径取决于心轴的尺寸,而外径则根据缠绕在心轴上的树脂和增强材料的量而变化。管道各层的纤维丝的方向需要精心设计,以提高重量而不降低阻力[ 20 ]。在离心铸造工艺中,树脂和增强材料被放置在旋转的模具内。离心作用将树脂/纤维层相互压实。之后,激活树脂聚合并形成管。使用离心铸造法,管的内径可以随着所用的树脂和增强材料的量而变化,而外径是固定的。这种方法可以生产出高质量的管,但需要大量工作并且在成本方面不具竞争力。Fiberspar Line Pipe™ 和复合增强线性管 (CRLP) 代表了两种相对较新的用于天然气输送的复合管。CRLP 由涂有或包裹在连续复合材料外壳中的钢管组成,这增加了钢管的强度和保护性 [ 2 ]。Fiberspar Line Pipe™ 是一种玻璃纤维增强环氧层压管。这种管的直径目前为 1-1/4 至 4 英寸,压力值范围为 750 至 3000 psi(约 50 至 200 bar)[ 22、23 ]。用于输送石油和天然气的钢管对腐蚀和随后的故障高度敏感。水下条件和海水环境中的氢氧化物和氯离子会加速导致金属泄漏、裂纹和断裂的过程。作用在这种部件上的巨大压力会加剧损伤的演变。由于腐蚀和金属损失是海上管道损坏的主要原因,因此修复它们对石油和天然气工业至关重要。因此,过去几十年来,世界各地都对这一主题进行了深入研究。损坏管道的传统修复技术包括移除损坏部分(或整个管道)并用新管道替换。作为替代方案,损坏区域用一层焊接钢覆盖。换句话说,外部钢套被焊接或固定在管的外表面上。焊接钢是一个繁琐的过程,尤其是在地下或水下进行时。因此,人们付出了巨大的努力来寻找有效和安全的修复解决方案。随着工作压力和管道损坏位置的增加,修理和维护的成本和技术问题会大大增加。因此,需要相对较轻且更易于使用的替代材料。增强纤维复合材料由于重量轻、强度高、刚度高、耐腐蚀性好、在疲劳载荷条件下性能优异,已被提议作为修复这些管状结构的最佳替代方案 [ 21,24 ] 。目前,通常用于此类干预的复合材料包括作为增强材料的E玻璃、芳纶或碳纤维以及作为基质材料的热固性树脂(聚酯、聚氨酯、酚醛树脂、乙烯基酯或环氧树脂)。根据具体的管道修复方法,目的是防止腐蚀区域进一步扩大、恢复受损管道的承载能力、避免受损区域的液体泄漏,或两者兼而有之 [ 24 ]。通常采用两种方法来修复故障管道,一种是基于湿法铺层,另一种是基于使用预固化层。湿法铺层包括使用直接原位浸渍的纤维来修复受损区域。使用能够在水下聚合的特殊环氧树脂作为基质。另一种方法是将环氧基树脂体系和碳纤维与柔性壳一起使用。假设复合材料壳的厚度固定,与 E 玻璃纤维增强材料相比,碳纤维沿圆周方向取向,可为支撑钢管提供增强的强度。预固化层技术包括使用预浸渍复合材料,以避免在受限且不易接近的空间内进行水下树脂固化而导致的问题。这种方法主要用于损坏局限于直管段的情况 [ 24 , 25 ]。上述方法可以组合或混合使用,以(至少部分地)解决单独影响它们的缺点。一个例子是使用碳半壳进行原位浸渍,而不是使用逐层重叠纤维片的传统方案。迄今为止,由于 FRP 修复材料在应用中存在实际挑战,金属套管仍然是最常用的解决方案。在海上领域,FRP 还被考虑用于生产各种主要和次要结构。安装在浮动工厂上的主要或关键结构包括立管和钢筋。浮动平台上的次要结构可以用复合材料制造,包括直升机桥、管道系统、住宅、人行道、楼梯。立管和钢筋是将浮动平台连接到海底结构的柔性系统。如果海床深度较大,此类平台通常是由废弃油轮改装而成,因为这样可以降低实现成本并可以储存原油[ 26、27、28 ]。图 3描绘了带有立管和钢筋的浮式结构张力腿平台 (TLP) 的示意图。图 3. 张力腿平台(TLP)示意图[ 29 ]。立管是将海上浮动设施或钻井平台连接到水下钻井和生产系统的管道。立管被认为是海上管道中最关键的部件,在严酷和恶劣的工作条件下承受高静态和动态载荷。连接管的长度和柔韧性对于承受由波浪运动和海流作用引起的水下结构和浮动站之间的相对位移至关重要。此外,立管还充当将原油从油井输送到地面工厂的管道元件的框架,并充当漏油时的容器。作用在立管上的载荷性质非常不同(集中而非分布,静态而非动态),并且沿其长度施加不均匀。集中力和扭矩主要作用在立管与浮动平台的连接处。另一方面,分布载荷归因于立管的重量和(内部和外部)流体结构相互作用。除了重力和浮力作用外,立管材料通常还要受到立柱上部的轴向牵引力、水流引起的径向牵引力、内部流体轴向(垂直)流动引起的剪切应力,以及影响浮式平台运动的集中力[ 30,31 ]。自 20 世纪 80 年代以来,人们进行了多次尝试,试图用 FRP 立管取代钢立管。20 世纪 80 年代,法国石油研究所 (IFP) 和法国宇航公司进行了一项先驱研究,测试复合材料海上管材。分析表明,闭合和窒息管线占立管总质量的 30%。用复合材料管线替换它们可将总质量降低 24%,从而减小作用在立管上的动态力。此外,重量减轻还可以减轻海流载荷的影响[ 30 ]。20 世纪 90 年代中期,美国商务部通过国家标准与技术研究所支持的先进技术计划 (ATP) 的投资,启动了一项相关计划,以开发、生产和测试大型复合材料结构。两个项目获得资助,研究 FRP 立管在深海水中的应用,分别侧重于钻井立管和生产立管[ 30 ]。尽管具体应用的要求各不相同,但这些项目都提出了共同的要素,旨在评估预测故障模式和极限条件的分析方法的可靠性,创建可靠的数据库来报告静态和疲劳性能,证明制造路线的稳健性,定义生产计划和成本评估指标。复合材料立管的商业应用可以追溯到 2000 年代。如今,出于安全考虑,钢制立管不能应用于超过 1000 米的深度。另一方面,与钢(或钛)立管相比,FRP 立管的质量要低得多。事实上,先进复合材料是深度超过 1500 米的唯一合适的立管材料。碳纤维是这些结构中最常见的增强材料,具有高强度和变形模量。它们通常与混合复合材料中的玻璃纤维结合使用,以降低成本。芳族聚酰胺纤维也被使用。加固结构并非严格纵向的。纤维沿立管的整个长度方向和周向排列,呈螺旋状[ 25 , 28 , 32 ]。如上所述,立管传统上采用金属材料制作。因此,恶劣的工作环境导致的严重腐蚀损坏非常常见。因此,当不需要更换整个立管时,建议使用复合材料修复立管,类似于混凝土和钢结构修复时的情况。多项研究表明,聚合物基纤维增强复合材料可有效用于修复钢管。C. Alexander 在他的研究 [ 25 ] 中调查了 E 玻璃和碳纤维复合材料与聚氨酯和环氧树脂在不同修复策略中的使用情况。使用单向碳纤维和环氧树脂可实现最高的拉伸承载能力和轴向刚度。相比之下,这种解决方案是最昂贵的。材料和制造策略的选择因情况而异,取决于机械性能和经济便利性之间的权衡。原则上,玻璃、碳纤维和芳纶纤维可用于修复。柔性湿法铺层和预固化分层系统已成功用于立管修复[ 24 ]。然而,这些复合材料修复策略存在与水下管道修复中讨论的类似的局限性。除了立管之外,浮动平台(深度超过 300 米时首选)使用所谓的支撑组进行支撑和固定。它由拉杆、绳索和筋腱组成。这些组件采用复合材料制成,提供了一种易于运输和安装的解决方案,可以使用普通船舶代替重型起重船。从海底到水面测量的最深 TLP 是 [ 26 ]:连接单元的主体由平行线材构成,这些线材由拉挤碳纤维杆制成,可确保出色的柔韧性、高变形模量和抗力。每组由 50-100 个桁架组成。组的最终大小由线材数量决定,具体取决于特定 TLP 所需的强度和刚度。尽管自 20 世纪 70 年代推出以来,碳纤维的成本已大幅下降,但在需要大量长拉杆的结构中,使用碳纤维仍然不经济。值得注意的是,对于安装在 5000 英尺深水中的单个 TLP,由碳纤维复合材料制成的锚固系统需要大约 220 万欧元的纤维。降低成本并保持承载能力的需求促进了基于碳纤维和芳纶纤维的混合复合材料作为增强材料的采用。环氧树脂是 TLP 肌腱中最常用的树脂[ 27,33 ]。沉箱是悬挂在海上平台上的大直径管道运输系统,用于吸入和分配海水,在各种工艺和公用设施中必不可少,如热交换器、海水淡化和净化系统的供水、废物运输和消防应用[ 34 ]。其直径从250到1200毫米不等,长度从20到100米不等,具体取决于平台的功能和大小。标准沉箱包括一个泵送和上升站,用于将海水输送到平台,以及一系列用于排放处理过的液体的较小管道。钢制沉箱对腐蚀过于敏感。因此,它们需要严格和持续的检查、维护和修理或更换程序,以确保符合安全法。这些程序通常包括水下检查,非常昂贵,其成本可能高达原始安装成本的五倍。许多海上供应商已经考虑将 FRP 作为沉箱生产中钢材的合适替代品。与传统钢沉箱相比,玻璃钢材料沉箱具有耐腐蚀、降低维护成本、重量减轻 50% 的特点,也使其更易于搬运和安装 [ 34 ]。钢材是石油和天然气工业中最常用的材料,因为它具有相当大的比重和良好的耐拖曳性,但它对腐蚀极为敏感。因此,为了确保海上部件的耐久性,避免与化学腐蚀有关的机械阻力损失,钢管必须配备有效的阴极保护系统,即牺牲阳极。由于铺设过程中的外部压力和弯曲应力,海底管道必须采用高机械强度的钢材(API 5L 级 X65 及以上)制造 [ 22 , 26 , 27 , 35 , 36 ]。一般而言,当压力是关键因素时,钢材优于玻璃纤维复合材料和塑料。钢管的压力值可能超过 5000 psi(即 350 bar),具体取决于管道尺寸和安装位置。高密度聚乙烯 (HDPE) 还可用于制造用于输送天然气和石油的管道,因为它具有出色的耐化学性。使用高密度聚乙烯 (HDPE) 管道输送天然气的压力限制在 100 psi(7 bar)以下。玻璃纤维/环氧 FRP 已在高于 3500 psi 的压力下进行了测试,直径为 2'' 至 3'' 的管道的压力为 2750 psi,直径为 4-1'' 的管道的压力为 2750 psi。硫化环氧管已成功通过 3750 psi(2 英寸)和 1100 psi(8 英寸)的认证。热塑性管道在高温下机械性能容易降低。对于 HDPE 管道,使用温度不应超过 100ºF(即 37 °C)的极限。FRP 材料的机械性能也会随着温度的升高而降低,但不如 HDPE 那样急剧下降。耐压玻璃纤维管的认证温度最高可达约 200ºF。纤维增强乙烯基酯管在高达 300ºF 的温度下仍能保持其性能,但一般来说,只有钢管才能承受高温。铸铁、塑料材料(例如高密度聚乙烯、PEAD)、玻璃纤维增强聚酯和水泥基材料也经常使用。混凝土管道很重,可以保证良好的耐磨性,但它们很难相互连接,并且对钢筋(钢筋)的腐蚀很敏感。铸铁管具有相同的作为钢管的优缺点,以及与连接相关的进一步问题[ 22,27,35 ]。增强聚合物复合材料被认为是一种比传统材料更有吸引力的替代品。这主要与优异的耐腐蚀性、高强度重量比和柔韧性有关。通过控制增强材料的类型、数量和方向来调整机械性能的能力使复合管成为高压条件下应用的理想选择[ 20、21、35 ] 。另一方面,它们在海底应用中必须加重(例如,水下管道),并且耐磨性较低。所用的树脂既有热固性树脂,也有热塑性树脂。热固性树脂在海上石油和天然气领域得到了广泛的应用,尽管它们通常比热塑性树脂具有更多的局限性。事实上,即使热固性树脂在原材料和制造方面相对便宜,但它们的保质期也受到很大限制。此外,它们比热塑性树脂具有更高的机械性能和热稳定性。另一方面,热塑性树脂表现出更好的耐化学性和更低的吸水率,这使得它们特别适合海上用途,同时还具有显著的可回收性[ 22 ]。表 2和表 3报告了典型的热固性树脂和热塑性树脂之间的定性比较。表 2. 石油和天然气应用中使用的热塑性塑料的性能[ 22 ]。表 3. 石油和天然气应用中使用的热固性树脂的性能[ 22 ]。“海洋可再生能源系统”类别包括安装在海洋环境中的设备和工厂,用于收集波浪、洋流、潮汐、盐度、温度梯度和风能。其中,潮汐能、波浪运动和海上风能代表了最成熟的技术,玻璃和碳纤维增强复合材料的应用越来越广泛 [ 37,38 ]。热能转换( OTEC )基于表面和深水之间的温差,通过热循环产生电能。热带地区更适合这种方法,因为这里可以达到更高的温度梯度。渗透势源于大陆地区海水和淡水之间的盐度差异。在流入海洋的淡水非常丰富的地方(如欧洲的波罗的海国家),渗透势是可能的。最后这两个概念仍处于理论规划阶段。波浪能来自电缆和波峰之间的重力势能差异。迄今为止,现有的波浪能技术根据相对于海岸的位置(海岸线、沿海地区、宽阔区域)和工作原理分为不同的类别。根据捕获波浪能的方法,设备分类如下 [ 37 ]:1. 振荡水柱 (OWC):这是一种部分浸没的结构,带有集成的气室,可将波浪引导到水线以下。由于流体的振荡,被困的水柱交替上升和下降,对气柱加压和减压,并将其推或拉通过涡轮机。它可以位于深水区的陆上或海上 [ 37 ],2. 溢流装置:它们由部分浸没的结构组成,将海水收集在水库中,水库的水位略高于周围的海面。该系统利用储存在滞留水中的势能,通过低水头水轮机将水流回海洋。装置可以安装在岸上,也可以漂浮在海上。浮动装置存在一些环境问题,比如系泊系统可能会影响底栖生物,或者海底电缆产生的电磁场 (EMF) 效应 [ 37 ],3. 振荡波浪浪涌转换器 (OWSC):它由一端固定在海床上的浮板组成,并与液压泵和涡轮机相连。该系统利用板块相对于固定点的振荡来直接捕获波浪能,而无需使用储水器或收集器。波浪将其机械能传递给浮板,浮板在运动中压缩液压泵,反过来,液压泵将储存在内部流体中的能量传输到涡轮转子 [ 37 ],4.点吸收浮标系统:利用波浪通过时漂浮物的升降来驱动液压泵并发电。这些装置漂浮在水面上,通过与海床相连的电缆固定就位。还有水下模型,即水下压差。在这种情况下,波浪的运动导致海平面上升和下降,从而引起水下浮标中的压差。它们的连续振荡运动驱动流体泵传递机械能[ 37 ],5. 衰减器:该装置的作用类似于浮标系统,由多个相互连接且垂直于波浪方向的浮动段组成。浮动段的相对振荡将波浪的能量转换为驱动液压泵的能量,从而产生电能 [ 37 ]。潮汐能由白天或半日规律周期产生。与其他可再生能源(如太阳能和风能)相比,潮汐能的主要优势之一是,由于潮汐行为已得到充分记录,因此可以长期预测能源产量。此外,潮汐波比风更加恒定,因此结果更易于量化 [ 37 , 39 ]。如上所述,由于海水密度高(至少是空气密度的 800 倍 [ 38 ]),相对于风力涡轮机,水下涡轮机要承受更大的工作负荷。此外,考虑到深海水区的难以进入,所用材料必须保持高强度和高刚度,能够耐受腐蚀性的海水环境,并且几乎不需要维护。出于这些原因,纤维增强聚合物复合材料,尤其是 GFRP 和 CFRP,是实现潮汐涡轮机叶片的一个有吸引力的选择 [ 39 ]。由于结构性能和低成本之间的权衡,GFRP 通常受到设计师的青睐。与 GFRP [ 39 ] 相比,CFRP 性能更高、重量更轻(叶片重量减轻约13 %),但成本却高出7/8倍。由于这个原因,碳纤维复合材料的使用仅限于叶片的主要部件 [ 39、40、41 ]。与风力涡轮机不同,水平轴潮汐涡轮机受到叶尖空化和较大叶片弯矩等问题的影响。特别是,GFRP叶片在其使用寿命(约20年)内会受到平均潮汐速度在2.4至4米/秒之间的影响,由于强大的弯矩导致叶片早期损坏。这些极端的工作条件将叶片尺寸的上限限制在12米左右。相反,CFRP可以显著提高最大可承受应力,使载荷远低于牵引(轴向)和剪切破坏应力。可以合理地得出结论,GFRP不是大型水下涡轮机叶片主要结构部件的合适材料[ 42,43 ]。如上所述,水下涡轮机难以进行监测和维护,因此叶片的设计必须能够长时间承受腐蚀性海水环境。除了与疲劳载荷有关的常见问题外,还需要仔细考虑电化学腐蚀现象以及海洋生物造成的污垢和损坏。先前的研究讨论了暴露于海洋环境对不同材料的影响,这些材料常用于高要求的应用(汽车、航空等),即[ 40、44、45 ]:经过一年的暴露,复合材料叶片表面的污垢程度很低,而金属部件则受到严重腐蚀,不锈钢材质的叶片除外[ 40 ]。风能生产不会产生任何固体、液体残留物或气体排放,也不会消耗任何形式的燃料。一些担忧与噪音和视觉干扰有关,或最终对动植物和野生动物的影响。这些因素阻碍了在居住中心附近安装风电场,但在一些地方,这些因素并不重要。显然,收获的电力很难预测,也不是恒定的,因为它取决于风速。海上风力发电厂面临的风速更高,而且通常为恒定风速,有可能将发电厂扩展到大面积地区,而不会受到与环境影响相关的限制。然而,与海上石油和天然气工厂使用的地基和支撑结构类似,暴露在腐蚀性海洋环境中的涡轮机和叶片的设计必须满足与近海风电场相关的额外限制。因此,海上风电场在材料、安装、维护和电网连接方面的成本相对较高。新技术、先进材料和制造工艺的最新发展使海上风电场的实现更加经济实惠和方便。一些研究指出,海上风电场的安装、使用寿命和处置所需的能源成本通常可在 6 - 12 个运行月内收回 [ 41,42 ] 。考虑到标准寿命约为 20 年,生产和消耗的能量之间的比率(效率系数)在 20 到 40 之间波动。维斯塔斯风力系统公司 [ 42 ]开展的研究显示,现代 3 兆瓦 (MegaWatt) 电厂的生产、安装和处置所使用的能源应在约 6.6 个月(地面安装)或 6.8个月(海上电厂)内达到盈亏平衡点。假设使用寿命为 20 年,两种情况下的能源效率约为 35 [ 37,46 ]。叶片通常采用多材料结构制造,结合增强纤维聚合物和木材,以满足强度、刚度和轻量化要求。增强材料通常是玻璃、碳纤维或混合织物。聚酯、乙烯基酯或环氧树脂用作基质。对于潮汐涡轮机叶片,上部和下部是分别生产的,然后通过粘合层相互连接,形成夹层结构(见图4中所示的示意图)。粘合强度和耐久性是至关重要的参数,因为它们会显著影响叶片的性能。碳纤维和玻璃纤维增强复合材料是制造海上风力和潮汐能设备叶片的合适金属替代品。事实上,FRP 具有高比强度和刚度,同时具有出色的抗腐蚀、防潮和抗疲劳性能。此外,它们可以模制成复杂的形状,同时减轻总质量。风力涡轮机和陆上和海上设备的复合材料叶片的设计和制造具有相同的要求。然而,潮汐涡轮机叶片浸没在海水环境中,因此在设计阶段需要更多关注形状的定义和材料的选择。事实上,潮汐涡轮机在其使用寿命期间(大约 20-25 年,与风力涡轮机一样)必须承受极端静态和疲劳载荷。疲劳载荷取决于安装深度、海床的接近度和波浪运动。因此,它们变化极大,难以预测。已经开展了大量的实验和数值研究,以研究循环载荷(特别是平均应力和施加载荷的可变幅度)对海水环境中复合材料降解的影响[ 44,45 ] 。此外,潮汐涡轮机的设计必须能够避免在其使用寿命期间进行维护,因为运行环境难以接近(通常涡轮机放置在约50米的深度,海流速度可能达到约 4 米/秒)。最后,需要具有很强的抗生物降解性才能抵御恶劣的海水环境[ 39,42,47 ] 。采用碳纤维和玻璃纤维作为复合材料的增强材料是出于材料成本和制造成本之间的权衡,以使生产的能量具有竞争力并满足设计要求(例如叶片的流体动力学轮廓)。成本最小化的需求促使设计师仅在结构的主要承重部件上使用碳纤维。环氧树脂和乙烯基酯树脂通常用作基质。前者与其他树脂相比表现出优异的性能,尤其是在循环载荷条件下。后者价格较低,且具有更高的抗水渗透性。与玻璃纤维复合材料相比,碳纤维增强材料被引入叶片以提高刚度和抗拉强度。然而,与总成本的上升相比,抗压强度的提高要低得多。因此,使用玻璃纤维和碳纤维的混合物,主要使用碳纤维来增加刚度,代表了这些竞争目标之间的妥协。对采用 E 玻璃纤维增强的环氧树脂和乙烯基酯树脂层压板进行的试验表明,在干燥样品上施加面内疲劳载荷的情况下,不考虑孔隙率、孔洞和层间脱落,环氧树脂/E 玻璃纤维板的抗疲劳性比乙烯基酯/E 玻璃纤维板高 25% [ 47 ]。其他研究表明,玻璃纤维增强乙烯基树脂在海水中老化后的静态性能降解程度低于环氧树脂 [ 46,48 ]。使用 FRP 的另一个担忧是其可回收性差。热固性树脂不能回收,含有这些树脂的复合材料只能通过焚烧处理。另一方面,热塑性树脂硬度高,可回收性更高。然而,叶片生产需要较高的工作温度,成品件的粘合可能很困难 [ 42 ]。如今,对环境的关注正在推动高度可回收材料的发展,如天然纤维素纤维和生物基聚合物。事实证明,碳纤维增强复合材料是更能抵御海洋环境的材料:碳纤维复合材料在 10 个月后显示出组件外表面上沉积的污垢百分比最低。此外,测试表明,材料的表面处理会影响粘附在转子表面上的生物百分比:如果表面粗糙或有裂缝,则粘附在转子表面上的生物百分比会更高,从而促进污垢的形成,相反,如果表面光滑,则粘附在转子表面上的生物百分比会较低。结果还表明,生物污染是累积的:当表面受到一定程度的污垢或腐蚀影响时,它会变得更容易受到影响。与 CFRP 相比, GFRP 更容易受到腐蚀和生物污染,但由于成本降低策略,它们仍在使用。为了解决这个问题,需要进行后制造工艺,例如镍磷电解沉积 [ 48、49 ]。这些工艺可以提高材料的表面光洁度,降低孔隙率、表面硬度和耐腐蚀性,保护材料免受氯离子的侵蚀。首批大型纤维增强塑料涡轮叶片是通过预浸料手工铺层制成的。潮汐涡轮叶片的主要部件(即上下蒙皮和箱形截面翼梁)是分开生产的,然后用粘合剂将它们连接在一起,生产成本非常高。人们采用了树脂灌注工艺来降低成本,从而减少需要组装的部件数量并提高工艺自动化程度 [ 46,48 ] 。树脂灌注工艺已经应用于风力涡轮机叶片的生产,但为了获得最终产品,仍然需要将叶片的上下蒙皮用粘合剂连接起来。西门子专利的“整体叶片”工艺是一个例外:它使用封闭的外部模具和灵活可扩展的内胆来同时生产整个玻璃/环氧树脂叶片。Airborne Composites 公司正在采用类似的技术来制造潮汐涡轮机叶片。他们使用 VARTM“一次性”工艺生产了 4 米长的叶片,安装在由欧洲海洋能源中心 (EMEC) 自 2014 年以来开发的 500 kW CoRMAT 涡轮机上。VARTM“一次性”工艺可确保更高的生产效率,消除了连接器接口周围的多余材料。该公司还开发了一种方法,在叶片根部加入插入件,并在树脂灌注之前将其连接到轮毂。因此,无需在成品复合材料上进行钻孔操作,并且层压板的厚度也减小了 [ 46 ]。一些与层压板质量和制造部件缺陷有关的问题仍未解决。对于单层层压板和夹层结构,制造缺陷包括分层、干燥区域和未润湿纤维、孔隙率、皱纹、纤维增强缺陷、纤维错位。由于需要监测的区域大、形状复杂、难以进入内部以及可检测缺陷种类繁多,无损检测是检测风力涡轮机部件制造缺陷最有效的技术 [ 42,50 ] 。近年来,FRP 的无损检测取得了相关进展,但仍然存在重大挑战。目前,视觉和超声波技术是最常用的方法,甚至不能提供全面和详尽的检查。因此,通常采用不同控制技术的组合。除了制造过程中产生的缺陷外,监测涡轮叶片在工作寿命期间的衰减(即疲劳损伤演变)以及检测由雷电和冰雹等意外事件造成的损坏发生率也至关重要。正在开发基于声发射分析或使用光纤传感器的结构监测系统,允许连续跟踪材料和结构的退化状态,并通过损伤评估软件和模型预测剩余使用寿命。检测到退化状态的意外变化可用于启动转子叶片的检查、修理或更换[ 42 ]。采用先进传感器实现故障检测系统的优点总结如下[ 50 ]:水下结构(如混凝土或金属柱)的修复是 FRP 在海洋环境中最常见、最有趣的应用之一。事实上,通过用浸渍树脂的纤维或织物包裹结构元件,可以轻松有效地实现约束和加固。最初,FRP 主要用于修复严重腐蚀的预压混凝土结构。后来,事实证明这些材料非常适合修复木质和钢制柱子。众所周知,腐蚀是混凝土劣化的主要原因。混凝土是一种碱性物质,pH 值在 12.5 至 13.5 之间。这种高碱性环境可保护钢筋,促进钢表面钝化。不幸的是,混凝土在其使用寿命期间会失去其保护特性。这主要通过三种不同的机制发生[ 21、46、51 ] :(1)二氧化碳与水泥中的碱发生反应,使混凝土孔隙内的水变得更酸,并降低 pH 值。该过程破坏了钢筋表面的氧化膜,阻碍了钝化条件。这一过程称为碳化,从表面开始,逐渐向深处移动至核心,(2)在存在电场的情况下,交叉杂散电流会干扰钢筋,电流从钢筋流出的区域可能会破坏保护膜,(3)混凝土与含有氯化物的海洋环境接触。氯离子渗透到混凝土中并到达钢筋。如果临界氯含量超过钢筋表面,保护膜可能会局部破裂。受氯化物侵蚀的混凝土会腐蚀,使钢筋暴露在氧气和水的作用下。受大气侵蚀的钢筋会腐蚀并增加体积,导致混凝土保护层脱落。海洋环境加速了钢筋混凝土的退化过程,在特定区域(称为浪溅区)产生局部损伤 [ 46、51、52、53、54 ] 。由于潮汐周期以及海浪的冲击作用,该区域不断干燥和湿润。因此,柱子的表面从完全干燥变为完全潮湿。因此,化学和机械作用会促进混凝土保护层的剥落或分层。图5显示了混凝土使用寿命期间可能受到的不同损伤。FRP 修复系统具有两种作用:一是提供防腐蚀保护(非强化修复);二是作为混凝土结构的加固(强化修复)。在前一种情况下,树脂渗透到混凝土的多孔层中,阻止了富含氯化物和氧气的水进入水泥和钢筋中,从而防止钢筋氧化。此外,沿纵向和横向放置的增强纤维增加了抗剪和抗弯强度,并避免了由于压缩作用而导致的柱截面扩大。因此,增强纤维既增强了混凝土的作用(在压缩作用下起作用),也增强了钢筋的作用(在剪切和弯曲作用下起作用) [ 46、52、53 ] 。最常用的 FRP 修复系统是 Tyfo ® Fiberwrap ®系统(Fyfe Co. LLC,加利福尼亚州圣地亚哥,美国)[ 52,53,55,56,57,58 ]。通常采用两种不同的方法,分别基于预浸料和湿法铺层 [ 52,53,55,59 ]。前一种方法需要在待修复的支柱表面放置由预浸料制成的增强套。通常使用可用水活化的聚氨酯树脂。当修复涉及使用预浸料时,可以采用碳纤维和玻璃纤维作为增强材料,否则,在湿法铺层的情况下,仅建议使用玻璃纤维,因为干碳纤维的现场定位(尤其是在水下)会带来一些问题并且过于耗时。预浸料层将以这样的方式放置在柱子上,即纤维沿着柱子的纵向和横向排列:纵向纤维增加弯曲强度,而横向纤维则承受压缩载荷并避免柱子截面变宽(它们增强了混凝土柱对膨胀力的抵抗力)。双向织物通常优于单向纤维,因为它们可以提供对两种载荷的支撑,从而最大限度地减少所需的层数并尊重修复结构的空间限制。通常,玻璃纤维复合材料层的数量是碳纤维的两倍,因为后者具有更好的机械特性。这些技术已成功用于修复和加固管道、桥梁和沿海或海洋结构,例如新加坡的滨海湾体育场。在这种情况下,使用了一种特殊的修复系统,该系统采用能够在水下聚合的玻璃纤维和树脂。这样就可以简单快速地安装织物,避免建造昂贵的临时结构来排水。如前所述,碳和芳纶纤维也可用作增强材料。在湿法铺层系统中,环氧树脂系统的选择取决于能否清晰区分柱子表面的干区和湿区。在这种情况下,可以使用两种不同类型的环氧树脂,否则,整个柱子上都使用疏水性环氧树脂。然而,由于潮汐的周期性变化,在两种情况下,第二种类型往往是首选。湿法铺层方法是一种更灵活的解决方案,因为可以根据预浸料中使用的标准堆叠顺序(例如 0°/90° 或 45°/135°)修改纤维排列,并且纤维织物的尺寸也可以轻松调整。然而,现场浸渍比预浸料方法更耗时,成本更高,因为需要额外的时间堆叠织物堆、树脂固化以及将灌注所需的所有设备运送到修复现场。在坦帕湾甘迪大桥和艾伦溪大桥上采用这两种方法进行的试验[ 51、52、53、55、59 ]表明:使用预浸料修复每个受损支柱大约需要 30/45 分钟,而通过湿铺层修复大约需要 90 分钟,在修复大部分干燥的柱子区域时,预浸料系统可以获得更好的效果,而湿铺层系统则可以在水下区域提供更大的成功保证。预浸料系统快速且用途广泛,也可用于紧急修复 [ 53 ]。为了令人满意地修复受损结构,必须在待修复基材和树脂之间形成足够的粘结。先前的研究强调,使用 FRP 进行修复的有效性与粘结强度密切相关:粘结强度低会导致修复效果不佳,防腐保护会在短时间内失效 [ 60 ]。在这方面,柱子的表面处理也是获得可接受粘结的关键因素。需要准确清除桩基上沉积的海洋生物以及从柱体上脱落的碎片或碎片,以确保 FRP 和基材之间紧密接触 [ 21,46,51,52,61,62 ] 。这样,水泥中的干净孔隙就可以被树脂填充。此外,必须清除钢筋表面的氧化铁,以中断氧化反应和腐蚀进程。包裹技术,即真空袋(或真空袋)和压力袋[ 46、55、58 ]已经开发出来,以确保在硬化阶段压力恒定且均匀。施加的压力既确保了增强材料和基材之间的粘结强度,又确保了支柱每个点的增强材料护套厚度几乎恒定。真空袋用于对 FRP 复合材料施加压力,从而形成真空(作用于要压实的材料的最大压力限制为 1 个大气压),无需模具和反模具,而是使用柔性隔膜(袋)和空气来施加压力。在固化过程中形成和维持气密密封至关重要,因为待修复基材的混凝土通常存在一些病变或裂缝,空气会从这些病变或裂缝中占据内部。另一个关键因素是从模具中去除多余的树脂。这必须在低粘度条件下进行,即在树脂达到凝胶点之前,以防止在硬化开始时对材料施加压缩载荷。真空袋的主要优点可归纳为去除层间空气、压实纤维层以有效传递力并防止纤维移动、降低水分以及优化复合结构中的纤维/基质比。压力袋技术由一个低阻力气密袋组成,气密袋外部为刚性或柔性结构。内部气密袋与压缩空气源相连。外袋由尼龙制成,带有垂直金属封盖 [ 58 ]。压力袋压法可以在包裹柱子的整个表面施加恒定且均匀的压实压力,并且大于真空袋压法的压力。通常,这两种方法都能够增强干燥和浸没区域的 FRP-混凝土粘结。每当需要使用更高的压力来压实 FRP 时,例如使用粘度更大的树脂类型时,最好使用压力袋压法。当使用环氧树脂时,与湿法铺层技术相结合也会更有效,因为相对较高的压力会促进树脂流入混凝土孔隙,从而提高粘结质量。另一方面,使用聚氨酯时最好使用真空袋压法,因为可以轻松去除树脂聚合过程中产生的气体(例如聚氨酯产生的二氧化碳),避免形成孔隙 [ 58 ]。混凝土是海洋环境中水下结构物使用最广泛的材料,然而,经过处理的木杆传统上被用于建造码头和海滨的其他结构物。木杆主要令人担忧的问题是海洋生物对其造成的损坏。这会缩短其使用寿命,并迫使其频繁维修和更换 [ 21 , 63 , 64 ]。出于对环境和人类健康的考虑,木杆的保护处理方法已经减少,因此目前需要有效的保护方法。海洋建筑中木杆的损坏源于物理和化学作用。前者主要与栖息在海床上的海洋生物、真菌和海洋蠕虫的作用有关,它们粘附在杆体上,使其腐蚀和变质。据观察,真菌会侵蚀水线以上的柱子,而木蛀虫主要存在于水下区域。因此,与混凝土柱(主要在浪花飞溅区受损)不同,木柱受损最严重的区域是浪花飞溅区正下方的潮汐区,这是由于真菌和蛀虫的共存所致[ 21,63 ]。图 6显示了木柱可能出现的损坏程度,具体取决于暴露在海洋环境中的区域。图 6. 泥线处的水下木柱照片(右)和木柱的典型损伤轮廓(左)[ 63 ]。冰、碎石、沙子等的机械作用也会降低柱子的完整性和使用寿命。使用 FRP 复合材料是修复木柱的可行解决方案。到目前为止,已经研究了促进基材与增强材料连接的不同方法 [ 63 ]:(1)用水泥填充钢筋和柱子之间的空间,水泥起到粘合剂和绝缘体的作用,(2)使用聚氨酯泡沫将受损部位与海洋蠕虫隔离,并填充支柱和复合材料之间的空间,与其他方法相比,水泥聚合物涂层技术在大多数情况下效果最佳,增加了钢筋和基材之间的摩擦力,从而减少了相对位移。然而,这一说法不能完全概括,因为负载和环境条件的变化可能会带来不同的策略。修复技术,特别是紧急修复技术,在不断发展,旨在开发新的适应性强、用途广泛的方法。到目前为止,已有多种纤维增强复合材料可用于有效修复受损的海洋结构物。例如,[ 54 ] 提出了一种可为任何支柱提供支撑的耐磨 FRP 护套。该解决方案包括一种可安装在受损支柱周围的涂层,无需使用预浸料层甚至原位浸渍纤维。使用沿纵向切割的高密度聚乙烯管,并沿横向排列玻璃或尼龙增强纤维。聚乙烯管非常灵活,无需使用铰链即可将其应用于支柱,也不会导致材料断裂。图 7显示了应用于木柱的增强护套的示意图。图 7. (a)支柱修复导管架示意图;(b)潮汐区内导管架安装示例[ 54 ]。涂层外部有起伏,这对于增加结构的刚度和强度以及便于连接和固定操作必不可少。增强纤维被放置在起伏内。基材和增强材料之间的连接由混凝土保证,混凝土可作为填料修复表面的任何裂缝并充当粘合剂。FRP 复合材料不仅越来越多地用作增强材料或修复材料,而且还被用作海洋环境中支柱建设的结构元素,取代铝、钢、木材和 PVC。最近的文献指出,目前使用的复合支柱有五种类型,如图8所示[ 65 ]:图 8. 复合桩类型:(a)混凝土填充 FRP 管,(b)SRP 管,(c)钢管芯管,(d)玻璃纤维增强塑料桩,(e)玻璃纤维拉挤管桩 [ 65 ]。涂有塑料外皮的钢柱,其中钢芯提供机械强度,而塑料外皮保护钢免受腐蚀。使用来自再生塑料材料的高密度聚乙烯 (HDPE) 作为涂层。洛杉矶港、圣地亚哥港和墨西哥埃尔索萨尔港都使用了钢芯管,然而,由于两种材料的热膨胀不匹配,观察到塑料外皮和金属芯之间出现分层问题 [ 65 ],结构增强塑料支柱采用挤压塑料基质和玻璃纤维或钢筋作为增强材料。增强元件以同心图案排列在内部塑料芯内,尺寸根据要支撑的应力类型确定。塑料外壳经过添加剂处理,以延缓降解,混凝土填充的 FRP 柱,其中 FRP 外壳填充无钢筋混凝土。FRP 提供结构防腐钢筋,压缩混凝土,同时隔离腐蚀性环境。另一方面,混凝土负责压缩区的内部阻力,并增强元件的整体刚度,与 FRP 外壳的屈曲形成对比,玻璃纤维拉挤管桩:外部由玻璃纤维格栅加固的 FRP 复合材料板组成,提供结构支撑。格栅插入物填充有聚乙烯、泡沫或再生塑料。在护舷桩应用中,填充物将外部纤维与插入物连接起来,以更好地吸收最终的冲击,玻璃纤维增强塑料支柱,涉及使用随机排列玻璃纤维的再生塑料。通常使用聚乙烯和 20% 的玻璃纤维。外壳致密而坚固,而塑料芯则填充泡沫以减轻总重量。还使用各种添加剂来增强材料的机械性能并提高其耐用性。本文报告了纤维增强复合材料在海洋环境中应用的最新进展。主要领域包括船舶建造、海上和管道、可再生能源设备和结构修复。在船舶建造领域,复合材料用于船体、船舶和潜艇,生产桅杆、螺旋桨和船舶和潜艇内部零件等部件。尽管复合材料早在 20 世纪 50 年代就已在海军领域使用,并在最近几十年得到了广泛传播,但金属仍然是各种应用的主要解决方案。事实上,船舶设计师和建造者对金属非常有信心,经验丰富,因此他们确保在各种应用中具有极好的性能。此外,复合材料的使用还存在设计规则、经验数据和优化大型海军结构设计所需的模型不足的问题。目前还没有可靠的分析工具来确定海军结构中复合材料的故障,特别是在爆炸、撞击、碰撞和火灾的情况下。此外,设计阶段固有的复杂性迫使人们采用保守的安全系数,导致 FRP 结构性能低下。在海上应用领域,复合材料既可用于修复立柱平台的管道或水下结构,也可用于建造天然气管道和浮动平台部件,如立管、钢筋和支撑结构。复合材料重量轻、机械性能高,且耐腐蚀性海水环境,已被证明是海上应用中金属的合适替代品。然而,金属仍然是管道和海上设备的主要选择。金属具有久经考验的记录,其在危险环境中的性能也得到了理解和证明。复合材料已用于风险不太大的领域(例如,在低压水管道中)。在可再生能源领域,复合材料主要用于建造利用海洋潮流和潮汐的设备,例如水下涡轮机和风能设备,例如转子叶片。该领域复合材料的发展是由承受海水环境中高疲劳载荷的需求推动的。然而,仍需要进一步研究,以开发新的树脂和纤维,以更好地满足风力涡轮机和其他海洋应用的要求,并优化这些设备的设计。特别是,特别关注获取有关复合材料性能和行为的可靠数据,以便开发可靠的结构设计模型,减少所需的实验测试次数。在修复领域,复合材料可有效用于修复因化学药剂和海洋生物而受到腐蚀的海洋环境的结构,例如钢筋混凝土、钢材或木材。海洋产业对上文讨论的领域越来越感兴趣。根据所分析的文献,可以概述进一步的考虑。就复合材料在石油和天然气工业中的应用而言,目前的文献强调了使用 FRP 作为标准钻杆作为钢管的合适替代品,因为它们重量较轻(仅为类似钢钻杆的一半)。迄今为止,由复合材料制成的智能钻杆正在开发中,这种钻杆能够在管壁内承载用于实时信号和电力传输的电缆。美国能源部和先进复合材料产品与技术公司制造了一些原型。仅在 2010 年底才公布了有关疲劳、扭转和拉伸测试的初步结果,并提出了几种设计方案。然而,还需要进行更多的研究来推动智能复合材料钻头在工业中的应用。在 TLP 结构中,复合材料主要用于制造立管和筋条。正在进行进一步的研究,以扩大 FRP 的使用范围,使其也用于生产 TLP 系绳、阀门和泵以及钻塞。尤其是,用作阀体和泵体主要材料的玻璃钢和碳纤维复合材料,在恶劣环境和腐蚀性液体(如酸、汽油、化学剂等)中具有显著的耐腐蚀性和耐久性优势。人们正在考虑用玻璃和碳纤维与热塑性树脂(如 PEEK 和 PPS)一起制造钻井站固井和修井作业中使用的部件,以取代传统的金属部件。这些部件包括挤压封隔器、桥塞、着陆环和衬管刮水塞。近年来,已经成功应用了几种使用复合材料的管道修复技术,例如高级桩封装 (APE) 系统(BASF Building Systems,美国明尼苏达州沙科皮)、LifeJacket® 系统(Jarden Zinc Products,美国田纳西州格林维尔)或 PileMedic® 系统(QuakeWrap, Inc.,美国亚利桑那州图森),并且可以找到大量对其分析的文献。尽管如此,目前正在进行多项研究以扩大这些方法的适用性。这些研究涉及 FRP 桩修复性能的现场评估、FRP 对混凝土的阻隔性能的表征以及综合设计方法的开发。正在研究无损检测方法,以检测和评估 FRP-混凝土粘结的劣化。目前采用的最有前途的方法是热成像和探地雷达 (GPR)。然而,它们存在固有的缺陷。事实上,热成像可以检测到初始空隙,但无法识别粘结劣化,因为热导率对 FRP-混凝土粘结中即将出现的差异不敏感。通过空气、水和 FRP 材料之间的介电性能对比,可以使用 GPR 方法检测粘结异常。然而,这种方法不能用于导电材料,如 CFRP,因为它们的电导率更高。因此,人们正在付出许多努力来开发替代的无损检测方法,以便快速进行现场粘结评估。FRP 在桩修复中的应用不仅包括加固受损柱,还包括腐蚀控制。目前正在研究表征 FRP-混凝土系统的氧气阻隔和氧气渗透性能,但这些研究仍处于起步阶段。这些努力的结果可以更好地估计修复后的腐蚀速率并优化 FRP 的使用。由于初始成本高,且性能要求严格,例如抗空气冲击和水下冲击、防火、防弹等,先进复合材料在大型商用船舶制造中的应用已逐渐减少。然而,新材料和新制造工艺的开发正在不断减少这些障碍的影响,从而促进复合材料在该领域的更广泛应用。造船商和研究人员仍在处理的主要问题与复合材料船舶结构生产中使用的设计规则有关。事实上,与钢制船舶设计不同,复合材料结构的设计参数数量更多,例如增强材料(例如玻璃、碳或芳纶纤维)、结构类型(即夹层或单层层压板)、复合材料层压板的性质(例如各向同性、正交各向异性)、芯材。因此,在设计路径的早期阶段正确定义材料和结构对于设计师来说是一项至关重要的任务,因为正确的选择可能并不那么明显。目前正在进行多项研究,以调查复合材料船舶结构的设计选择如何影响其重量和成本。这些研究的目的是为了彻底了解造船厂针对各种船舶长度、载荷和结构部件所采用的潜在材料和结构配置之间的重量和成本差异,并确定在生产具有成本和重量效率的产品过程中的设计决策基础。
作者文献:
Conceptualization, P.C., F.R., A.N. and F.T.; methodology, P.C. and A.N.; investigation, F.R. and F.T.; resources, P.C.; data curation P.C., F.R., A.N. and F.T.; writing—original draft preparation, F.R. and F.T.; writing—review and editing, P.C. and A.N.; visualization, P.C., F.R., A.N. and F.T.; supervision, P.C. All authors have read and agreed to the published version of the manuscript.详情请点击https://www.mdpi.com/2077-1312/8/1/26链接前往查看。